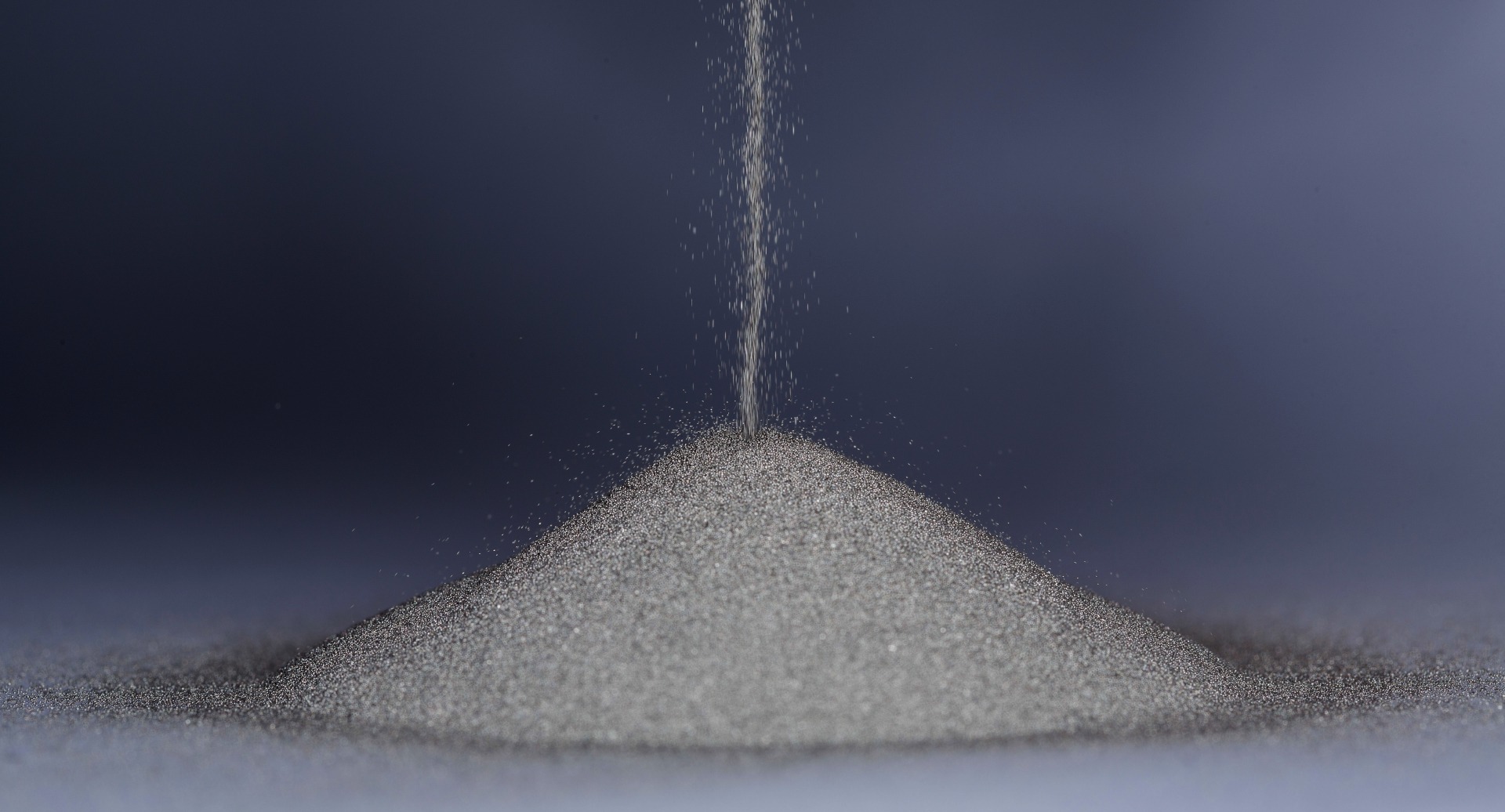
Electron beam powder bed fusion processing of pure tungsten
Why Tungsten?
Tungsten has the highest melting point of all the elements, 3422 °C, which makes it an attractive material for high temperature applications. Tungsten has several other desirable properties such as low thermal expansion coefficient, high thermal conductivity, low vapor pressure, radiation resistance, etc. and is, consequently, used in applications such as incandescent bulb filaments, electron emitters, x-ray generator targets, radiation shielding, etc. It is also a material of high interest in nuclear fusion reactor applications, which is an extreme operating environment, for parts such as plasma facing components.
Manufacturing pure tungsten components using traditional processes, such as casting, forging, rolling, joining, and machining, is challenging. One reason is that tungsten is brittle at temperatures below 300-600 °C. These challenges coupled with numerous benefits, especially the design freedom offered by additive manufacturing (AM), have triggered significant research interest in AM of tungsten in recent years. However, laser beam powder bed fusion (LB-PBF) has shown very little progress because it operates typically at low process temperature ~200 °C. So far, it has been impossible to manufacture fully dense and crack-free bulkier parts in pure tungsten with LB-PBF [1].
Why Electron Beam Powder Bed Fusion?
Electron beam powder bed fusion (EB-PBF) operates in vacuum and can easily maintain process temperatures above 1000 °C. The inertia-free deflection of the electron beam enables beam deflection speeds higher than km/s. These features allows EB-PBF manufacturing of crack sensitive materials through better thermal management and with excellent control of chemical purity. Recent research has successfully demonstrated fully dense and crack-free tungsten parts by EB-PBF [1,2] by keeping the process temperature so high that tungsten remains ductile. At Freemelt AB, EB-PBF process parameters have been developed for the industrial system eMelt for production of tungsten components. Tungsten is one of the three focus materials for Freemelt besides titanium and copper.
A dense and crack-free microstructure of EB-PBF processed pure tungsten from a part manufactured at Freemelt AB.
Most previous EB-PBF studies on tungsten have involved the conventional line melting strategy. Freemelt is also exploring spot melting strategies that are available with the proprietary Pixelmelt® software. Spot melting allows melting at higher beam power and is expected to further increase the productivity of tungsten parts in Freemelt’s industrial systems.
The electron beam source in Freemelt machines is a diode type source with a laser heated cathode. The advantage of this source type is its consistent beam spot quality throughout the entire beam power range 0-6 kW. Other electron beam source solutions on the market may have a spot quality that degrades quickly if the beam power is increased above 2 kW.
Freemelt’s unique solution enables development of an EB-PBF process that uses high power not only for the thermal management process steps but also the melting step. Using such high powers for EB-PBF melting is unprecedented. a few of the melt settings developed at Freemelt that produce dense crack-free pure tungsten parts to those in the published literature indicates the uniqueness of the process window that has been unlocked by leveraging capabilities offered by the electron beam source.
Spot size stability of the Freemelt electron beam source. Comparison of melting
speeds showing unique process window at high power.
[1] Zhang H, Carriere PR, Amoako ED, Rock CD, Thielk SU, Fletcher CG, et al. Microstructure and Elevated Temperature Flexure Testing of Tungsten Produced by Electron Beam Additive Manufacturing. JOM 2023. https://doi.org/10.1007/s11837-023-06045-5.
[2] Ledford C, Fernandez-Zelaia P, Graening T, Campbell Q, Rojas JO, Rossy AM, et al. Microstructure and high temperature properties of tungsten processed via electron beam melting additive manufacturing. Int J Refract Metals Hard Mater 2023:106148. https://doi.org/10.1016/j.ijrmhm.2023.106148.
2023-11-27 15:33:39