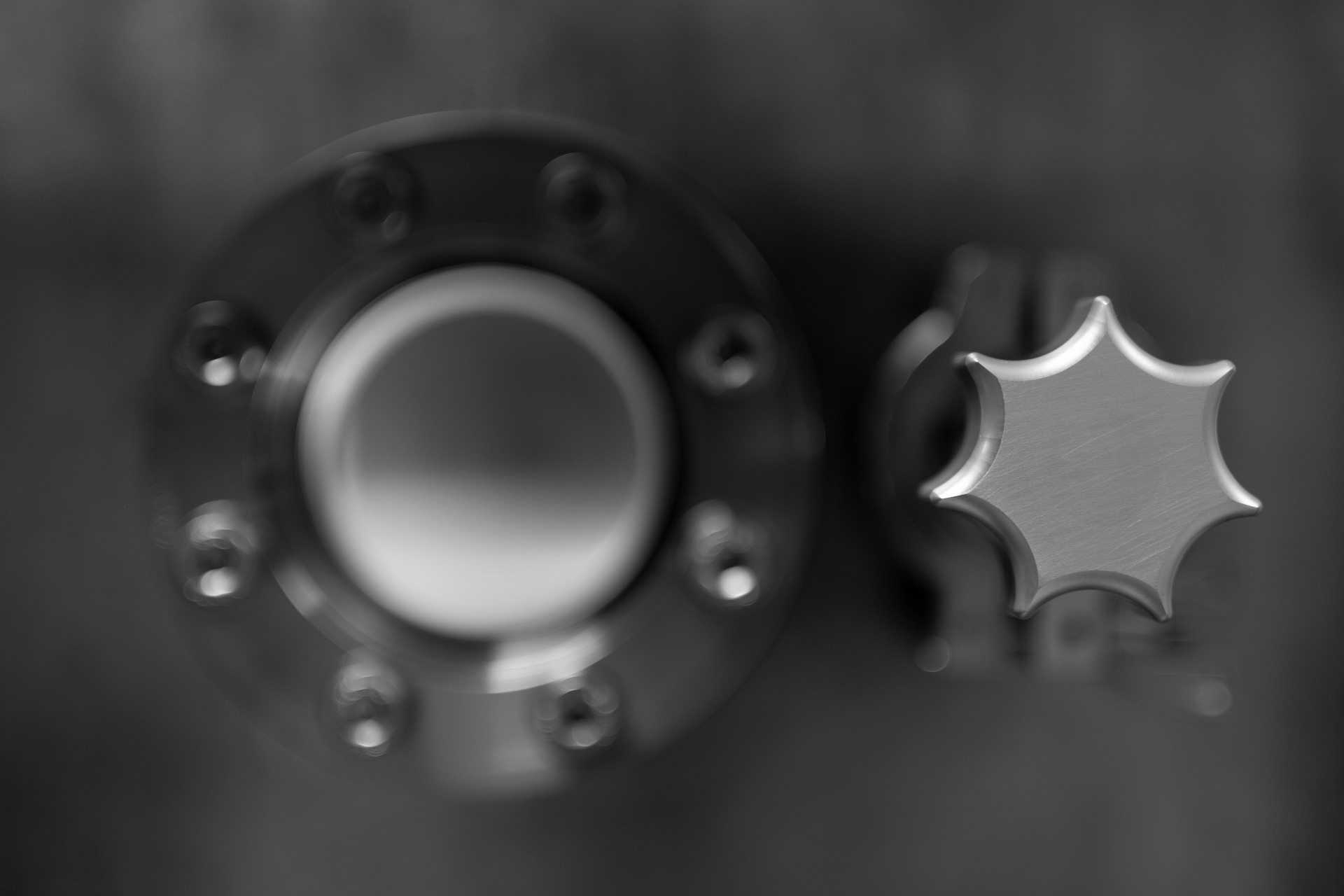
Nine myths about Electron Beam Powder Bed Fusion
A myth is a widespread idea or story which is believed to be true, but on closer inspection turns out to be unproven, false, or only half-true. I have been involved in Additive Manufacturing (AM) and specifically Electron Beam Powder Bed Fusion (E-PBF) for quite some time. Below I will share nine myths about E-PBF that I frequently encounter.
Myth 1: E-PBF is a subdivision of L-PBF (Laser Powder Bed Fusion).
False. E-PBF and L-PBF are two different AM technologies of equal status. Both belong to the PBF category of AM, and both exist for good reasons since they have different strengths and weaknesses.
Myth 2: E-PBF is very similar to L-PBF.
Well, at first glance E-PBF and L-PBF may appear similar, since they are both based on layerwise melting of metal powder with an energy beam. But if you look closer there are lots of differences, for example:
- The physical interaction with solid matter is different for electrons and photons (light). Photons give off their energy at the very surface, whereas electrons have some penetration depth into the material. Energy efficiency can also be very different for electrons and photons, depending on the material to be processed. These factors affect material properties and productivity.
- E-PBF takes place in vacuum whereas L-PBF (usually) runs under protection of an inert gas. These different environments strongly affect melting characteristics, purity, evaporation, cooling, etc.
- E-PBF usually operates at much higher temperatures than L-PBF. This gives different material properties in terms of internal stress level, microstructure, tensile properties, crack sensitivity, need for heat treatment, etc.
- E-PBF usually requires a slight pre-sintering of the whole powder bed which has implications on the need of support structures and also on post-processing.
Myth 3: E-PBF is for titanium alloys only.
Well, it is true that E-PBF is closely associated with titanium alloys, but this is mainly for historical reasons. Titanium was tested at an early stage, turned out to work well and rapidly became the material of choice for E-PBF. However, this does not mean that titanium possesses magical properties for E-PBF.
There are many other materials that have great potential to work with E-PBF, as proven by numerous small-scale tests at universities and research institutes. We just need to work together to bring other materials up to the same E-PBF maturity level as titanium.
Myth 4: E-PBF always gives higher surface roughness than L-PBF and other AM technologies.
Unproven. Personally, I believe that the main reason for higher surface roughness is the coarser powder and the thicker layers traditionally used with E-PBF. Few attempts have actually been made with finer powders and thinner layers. High productivity and low powder cost have been stronger driving forces than surface quality. Thus nobody really knows how smooth surfaces E-PBF can give under optimum circumstances.
Myth 5: A drawback of E-PBF is that the finished build needs several hours of cooling time.
Well, since E-PBF is a hot process under vacuum, it is natural that some cooling time is needed, particularly for reactive materials that cannot be exposed to air while hot. But why is the cooling time itself considered a drawback? At the end of the day, AM productivity is determined by the total turnaround time per part manufactured in an AM machine. The cooling time is just a fraction of the total turnaround time, and it will in most cases be well compensated by the high build rate of E-PBF.
If you run a race, it is your total time that defines your performance, not your speed in various parts of the race.
Myth 6: E-PBF only works with coarse (>50um) metal powders.
False or unproven. This is a widespread belief originating from “smoke” issues observed with fine powder in the early days of E-PBF. In reality, the reason why coarse powder has been preferred is that E-PBF is capable of melting coarse powder. Coarse powder is cheaper, safer and easier to handle. As mentioned, few E-PBF attempts have been made with finer powder. I am aware of only one paper describing tests with 25-45um titanium powder, and those tests were successful.
Myth 7: E-PBF only works with spherical powders.
Unproven. I claim that the reason why spherical powder is needed is more associated with the actual design of powder feeding and powder layering systems than with the E-PBF process itself. There is a huge R&D opportunity for improvements and innovations in powder distribution which could lead to higher tolerance to powders of irregular shape.
Myth 8: E-PBF material always has columnar microstructure.
False. E-PBF microstructures are strongly dependent on beam parameters. It has for example been demonstrated that equiaxed microstructure can be obtained by innovative beam scanning algorithms. This is very much an unexplored R&D territory. In the future, I believe it will be possible to tailor the microstructure locally in different regions of one single E-PBF component.
Myth 9: E-PBF does not work with magnetic materials.
False or unproven. This belief originates from the fact that an electron beam is easily perturbed by a magnetic field. Ferromagnetic metals like iron, cobalt and nickel can indeed have some permanent magnetization at room temperature. However, keep in mind that the ferromagnetic properties are lost above a certain temperature, the so-called Curie point. Thus, in an E-PBF process at elevated temperatures, ferromagnetic materials are not necessarily an issue.
2020-02-19 13:19:23
Author: Ulf Ackelid, Principal Scientist, founder Freemelt AB